Thermochemical Conversion.
Thermochemical conversion refers to the decomposition of organic matter of biomass for the production of biofuels including liquid, gaseous, and solid fuels. Thermochemical conversion can be classified as pyrolysis, liquefaction, gasification, and direct combustion based on their temperature, pressure, and duration of heating. Thermochemical conversion is considered as the simplest route for biomass conversion into biofuel when compared to chemical and biochemical process. In pyrolysis of biomass, the biomass sample is heated at 400°C to 600°C with a pressure of 0.1 MPa for 30–60 min in the absence of oxygen which mainly produces liquid oil, gas, and solid char. So far a wide number of studies investigated the slow and fast pyrolysis behavior of different biomasses with or without catalyst and reported promising results. The biooils produced from the pyrolysis of biomasses have a higher heating value of 31–42 MJ/kg with a viscosity of 0.060 Pa s and mainly contains hydrocarbons from lipids and nitrogenous compounds from protein.

More importantly, algal and wastes derived biooils are more stable compared to biooils produced from lignocellulosic biomass pyrolysis which is favorable for future applications. The conversion rate of biomass and the quality of biooils produced by the pyrolysis are influenced by temperature, pressure, holding time, type of pyrolysis, and catalytic effects .


Microwave Assisted Pyrolysis.
Microwave‐assisted pyrolysis (MAP) is a new thermochemical process that converts biomass to bio‐oil. The microwave technique is one of the most promising methods of enhancing and accelerating chemical reactions. The reactions can be completed more efficiently in comparison with other conventional methods due to effective heat transfer profiles. This is emerging as one of the best technologies in the pyrolysis process; it reduces residence time and accelerates chemical reactions, which leads to energy saving. In this section the microwave-assisted pyrolysis method has been reviewed extensively. Compared with the conventional electrical heating pyrolysis, MAP is more rapid, efficient, selective, controllable, and flexible. Microwaves are normally defined as the electromagnetic waves which consist of two perpendicular components, namely electric and magnetic fields.
Conventional thermal heating is known as a traditional heating system (with an external heat source such as an oil bath or heating mantle) where heat is transferred from the surface towards the center of the material by conduction, convection, and radiation. This heating system is relatively slow and inefficient and depends on the thermal conductivity of the material and convection currents. On the contrary, dielectric heating transfers electromagnetic energy to thermal energy; it is a kind of energy conversion rather than heating. The microwaves can penetrate materials and deposit energy, thus the heat can be produced throughout the volume of the materials rather than an external source (in core volumetric heating). The figure (in left) demonstrates the difference in mechanism for conventional and dielectric heating systems. As illustrated in this figure, the center of the material is at a higher temperature than the surrounding material in microwave heating, unlike conventional heating.
Hydrothermal Liquefaction.
Hydrothermal liquefaction (HTL), also refers to as hydrous pyrolysis, is a thermochemical depolymerisation process in an enclosed reactor to convert wet biomass into biocrude oil and chemicals at moderate temperature (typically 200–400°C) and high pressure (typically 10–25 MPa). Feedstocks such as biomass, food processing waste, manure, and municipal sludge typically have high moisture content and thus make HTL an appropriate process. In HTL processes, water serves as an important reactant. As the reaction condition approaches to the critical point of water, several properties of water are drastically changed and able to bring about fast, homogeneous, and efficient reactions . Because subcritical water has a leading role as a heat transfer and extracting medium, HTL is relatively independent of the size of biomass particles or heating rates. The product yield and physiochemical properties of an HTL are primarily affected by the types of feedstock, processing conditions (primarily reaction temperature and time), and existence of catalyst.

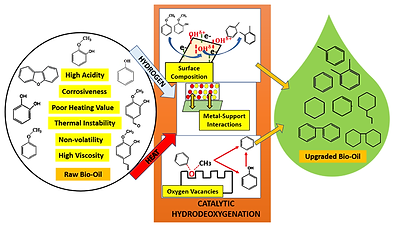
Catalysis and Hydrotreatment.
Catalysis is a branch of chemical kinetics of great industrial and commercial importance. Catalysis can be generally described as the action of a catalyst, which is a substance that accelerates the rate of a chemical reaction, while itself remaining unchanged by the reaction. Catalysts enable reactions to occur much faster and allow the use of milder conditions of temperature for achieving reaction rates of practical use. They achieve this by providing an alternative pathway of lower activation energy for the reaction to proceed. There are two main categories of catalysis: homogeneous catalysis, where the catalyst is in the same phase with the reactants, heterogeneous catalysis, where the catalyst is present in a different phase from the reactants in the reaction. Heterogeneous catalysis is often called surface catalysis as it mainly occurs between a solid surface and a gas.
Catalytic hydrotreating is a hydrogenation process used to remove the contaminants such as nitrogen, sulfur, oxygen, and metals from liquid fuels. These contaminants, if not removed as they travel through the processing units, can have detrimental effects on the equipment, the catalysts, and the quality of the finished product. Typically, hydrotreating is done prior to processes such as catalytic reforming so that the catalyst is not contaminated by untreated feedstock. Hydrotreating is also used prior to catalytic cracking to reduce sulfur and improve product yields, and to upgrade lower value compounds into high value chemicals.
Biomass & Fuel Characterization.
Biomass feedstock offers a wide range of fuel and fuel-blend sources with much interest on the liquid fuel. Characteristics of biomass feedstock vary greatly, and they negatively impact the quality of the fuels derived thereof. Furthermore, the characteristics dictate the choice of processing techniques employed in their conversion to value-added chemicals, which affect its characteristics. Therefore, it is essential to gain an in-depth understanding of the quality of biomass feedstocks by critically examining their properties via variety of techniques and methods. Biomass characterization addresses important feedstock material quality and performance issues such as chemical/elemental composition and variability, thermochemical feedstock properties, particle size characteristics and morphology, particle density and properties, hydrolysis, fermentation, and conversion performance.
Fuel characterization is the primary and a critical step in the evaluation of biomass and waste feedstocks' suitability for a thermal conversion process. Detailed and accurate characterization is especially important for proper utilization of inhomogeneous and low quality biomass and waste feedstocks, to prevent operational related problems, optimize conversion processes and design conversion systems.

OUR RESEARCH AREA & FOCUS